Table of Contents
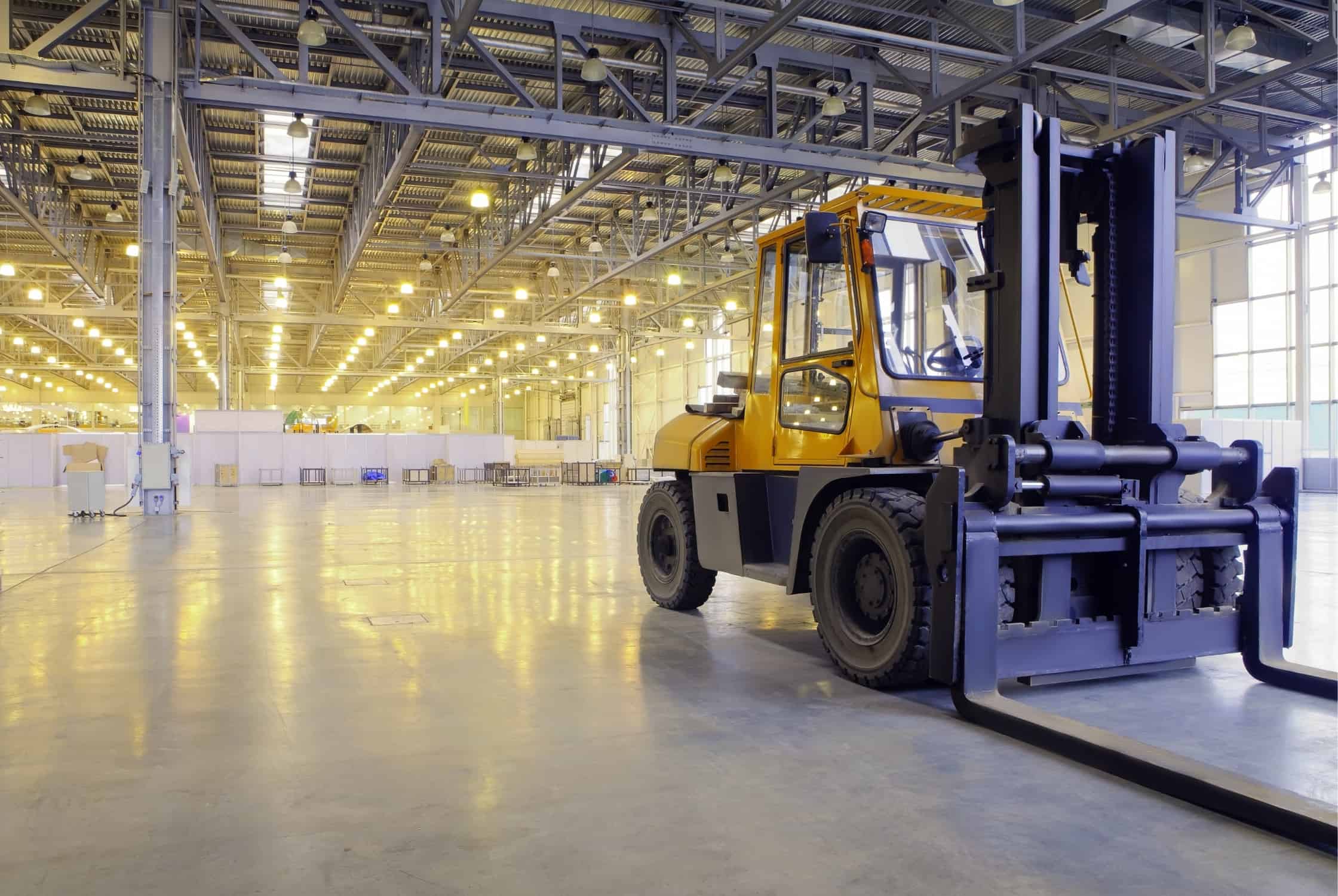
A forklift is heavy machinery designed to move pallets, store materials in designated spots, and allow the movement of items from shelves that can’t be done by hand. These machines are dangerous even when operated by the best-trained drivers. That’s why forklift safety and forklift training are vital to accident prevention. Caution combined with OSHA compliant training helps eliminate accidents. In this guide, you’ll learn why forklift safety is so important, the basics of forklift safety equipment, a few useful forklift safety tips, and how to implement forklift safety training and get your official forklift certification.
Why Forklift Safety is Important
Heavy machinery is dangerous. It’s that simple.
Forklifts are powerful machines, easily weighing thousands of pounds. The weight is distributed unevenly, making maneuverability tricky even in the best conditions. In addition, the forks, located at the front, restrict an operator’s forward view. Though heavy, forklifts can reach speeds approaching 20 mph making braking to a quick stop challenging.
That is why a forklift in motion is a safety risk in motion.
The Bureau of Labor Statistics compiled data in 2019 showing an astonishing 888,220 forklift accidents between 2011 and 2019. Seventy-nine deaths were reported in 2019 alone.
Some common consequences of forklift injuries are:
- Cuts/lacerations
- Bruises
- Broken or crushed bones
- Amputations
- Death
The leading causes of death from forklifts include:
- Rollovers (22%)
- Pedestrian collisions (20%)
- Crushed by forklifts (16%)
- Falls from forklifts (9%)
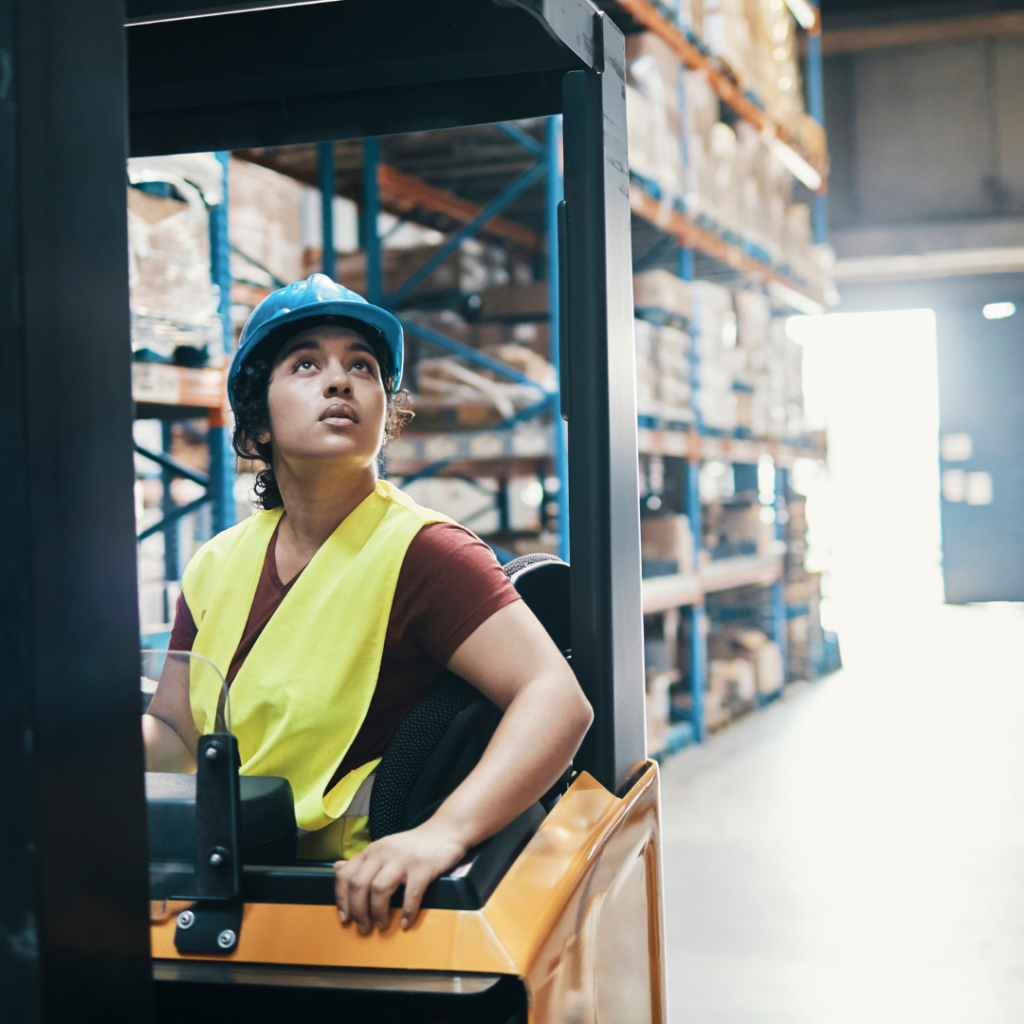
Forklifts are a danger to everyone at your company, and not just physically.
OSHA statistics show a forklift operator is the victim in 42% of fatal forklift accidents. This means nearly 60% of fatalities will be pedestrians or fellow workers. This all-encompassing risk is why the forklift “HALO” rule was implemented.
When rules like the HALO rule aren’t followed, the injuries aren’t limited to those who were directly involved in the accident.
It’s human nature to be shaken and disturbed when witnessing a fellow worker injured or killed. Those feelings can be even more intensified if you are directly responsible. The emotional and psychological trauma after an accident can shatter the sense of security employees have, leaving them struggling with anxiety, fear, guilt, and shock.
Companies are getting forklift safety wrong.
Do you want to know how we know that?
- Multiple complaints against forklift drivers
- Several near misses
- Numerous accidents
- Lost productivity due to employee injury
If employees are not properly trained, aren’t held to OSHA standards, and the company itself does not employ additional safeguards like safety lighting, warning signs, and forklift maintenance, in addition to warehouse safety standards, then there will be a much higher chance of severe injury and death.
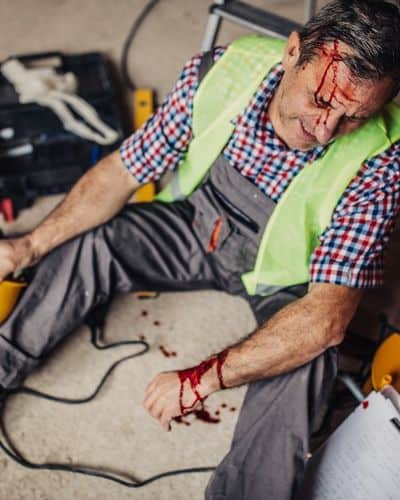
Forklift Safety Equipment
What is the most important safety feature on a forklift?
The operator.
If you were thinking the horn, lights, the halo rule, or various other options, you would be wrong.
The operator is the most critical safety feature on a forklift. A well-trained, aware, and experienced operator can safely lessen the dangers posed by careless operation.
Forklift Safety Lighting
Red and blue color-coded safety lights make forklifts more noticeable. They are a great precautionary measure to protect workers, especially in low-light conditions.
Red lights cast an illuminated area on either side of a forklift creating a no-go or danger zone. Pedestrians will easily see how far away they need to stand from the forklift.
Blue lights project a blue pedestrian light either in front, at the back, or whatever direction the forklift is heading. The warning beam projects up to fifteen feet, warning pedestrians that a forklift is operating.
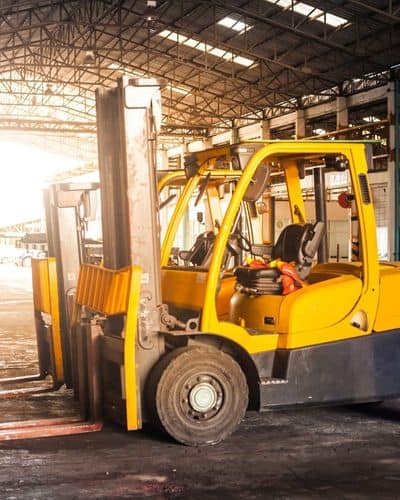
Forklift Safety Tips
The Basics Matter
When it comes to staying safe around heavy machinery and mobile equipment, it always comes back to the basics. Even high-tech fixes like a proximity alert system are installed to solve a basic problem. Daily forklift inspections should be a basic practice. Forklifts should be inspected at the start of your shift and regularly maintained to prevent untimely and dangerous equipment failure.
Another basic to always keep in mind is forklift class. Different types of forklifts have different limitations. An electric forklift will have more distinct requirements and capabilities than a gas-powered forklift. Standup forklifts differ from sit-down forklifts.
Here are a few of the most important forklift safety basics to keep in mind:
- Get a forklift certification
- Inspect the forklift daily
- Do not operate under the influence of drugs or alcohol
- Don’t raise or lower forks while the machine is in motion
- Don’t use the forklift to elevate other workers
- Honk when driving around corners
- Do not speed
- Maintain line of sight/awareness
- Be aware of the forklift class
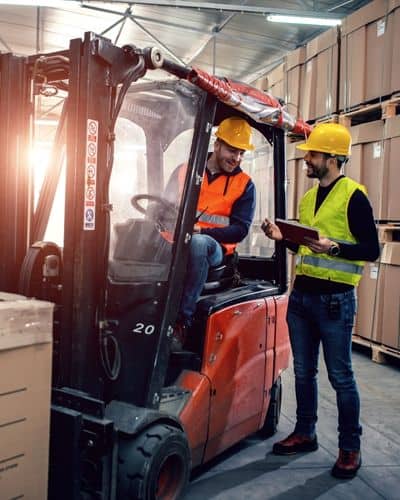
Falling Forklift 101
When a forklift is falling over, your first instinct may be to jump out to clear the impact zone. Fight that instinct. Jumping out can cause you to be pinned underneath, and the sheer weight of the forklift can crush you.
Always wear your seatbelt, it protects you from being thrown from the cabin. Stay in your seat, securely grip the wheel, and brace yourself with your feet, using your feet to push back into your seat.
Stick to the HALO Rule
The HALO rule was implemented to decrease fatalities and provide a standard to decrease all accidents. It consists of two zones:
The Danger Zone is within three feet of the forklift. If a pedestrian is within three feet of a forklift, the operator is required to stop.
The Warning Zone is located within six feet of a forklift. This zone requires equal focus by the operator and pedestrian. Both must make and maintain eye contact. The pedestrian should indicate their intention and the operator is required to yield the right of way.
Create a Forklift Safety Plan
A safety plan is only as good as its trainer. Make sure your “in-house” trainers are skilled. Also, make sure the safety plan complies with OSHA standards. Here is an OSHA recommended guide to developing your plan.
- Identify the equipment to be used
- Evaluate your facility’s hazards
- Establish your training methods
- Create your training program content
- Determine a valid employee evaluation
- Develop a documentation system
- Prepare refresher training
Forklift Safety Training
Forklift training is not only a way for operators to learn how to properly operate the machine but it’s a chance for the drivers to ask questions and gain insight into the ins and outs of its abilities and dangers. In-depth training helps drivers identify and address problems before they cause injury.
Are there training guides for forklift safety?
Yes. OSHA offers a warehouse/distribution written safety plan. This plan can be customized to your company and does include a Forklift and Industrial truck section.
Forklift Operator Qualifications:
- Be a U.S. citizen
- Be over the age of 18
- Complete a formal educational and instructional class that meets OSHA standards
- Complete a formal evaluation either in a classroom or online

Need to Know: Forklift Certification
Forklift certification is obtained through a training program compliant with OSHA policies. The certification can be completed in a relatively brief period. There are two avenues to gain certification.
- In-person certification involves classroom training and firsthand demonstrations with a forklift.
- Online certification is done by watching an instructional training video and then passing the exam. You then receive your OSHA certification and license. Your hands-on training will be received from your employer.
Forklift Certification FAQ's
Yes. OSHA requires recertification every three years. Refresher courses are recommended when an operator is involved in a near miss or actual accident.
No. Employers can be fined up to $250,000 for not certifying their workers. Imprisonment can happen if the violation is severe.
Yes. Companies that put their employees through forklift safety courses instill confidence while boosting morale. When employees feel valued, they will work harder to return the goodwill received from the company. The price of training and the time it takes to cultivate a safe environment are small investments to pay, especially when the dividends awarded are priceless.
SynTech believes safety improves productivity. We have over 40 years of experience making work sites safe for employees, and we are the #1 sales and service provider of forklift proximity detection systems.