Forklifts are powerful tools with many moving parts and require regular maintenance to keep them operating smoothly and safely. Regular maintenance on forklifts is unquestionably one of the most important concerns addressed by warehouse and factory workers to safeguard against accidents. Safety is not, however, the only reason regular maintenance is valuable.
Forklift maintenance benefits
Maximizes productivity: Broken down forklifts halt movement and organization of equipment and products. Preventive maintenance helps to spot problems and correct them before disaster occurs.
Helps maintain operating costs: Preventive maintenance costs are lower than the cost of emergency repairs that will be needed when equipment is not well-maintained. Equipment that is serviced regularly is more cost-effective on a month-to-month basis.
Allows a more effective schedule: Routine maintenance helps anticipate the life span of a forklift’s components. This enables the planning of repairs at a convenient time.
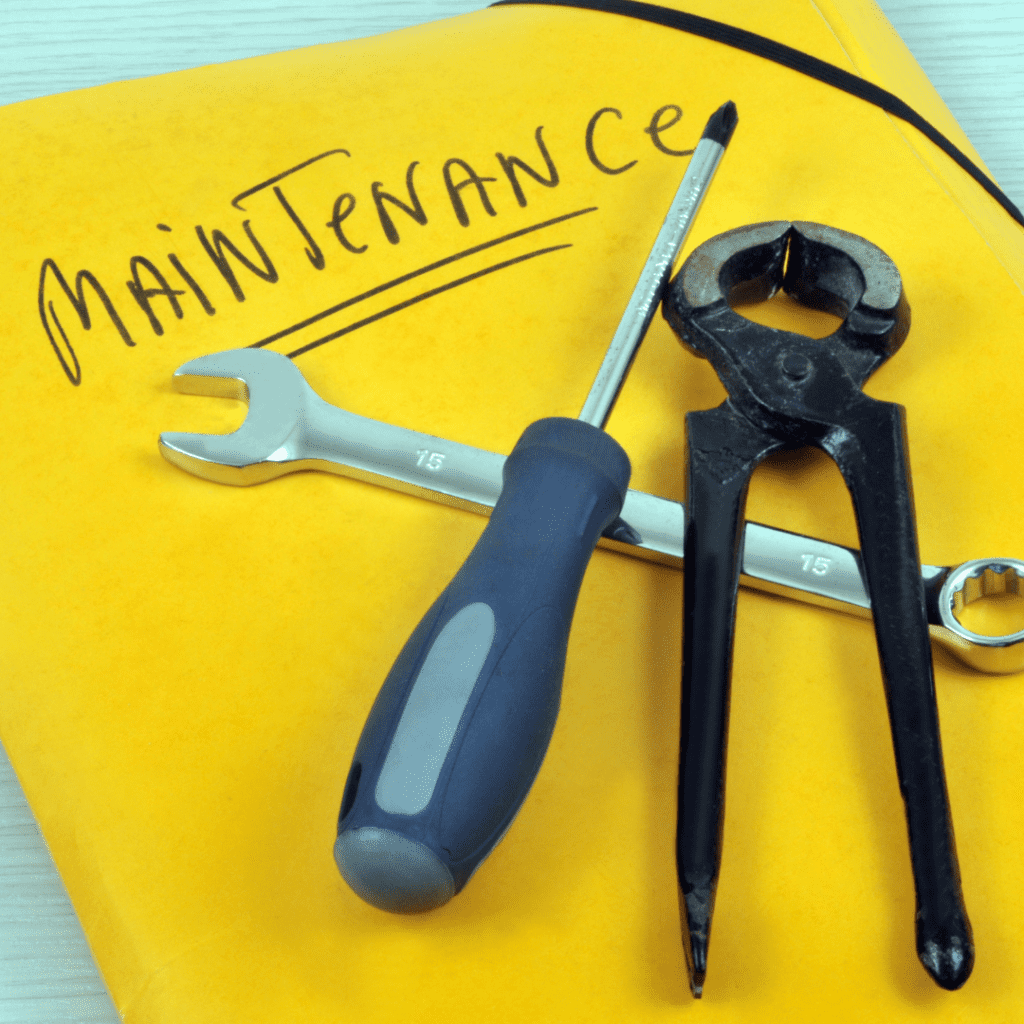
Essentially, well-maintained equipment is the backbone of continued efficient and accurate product movement throughout warehouses and fulfillment centers.
OSHA forklift maintenance requirements
The Occupational Safety & Health Administration (OSHA) has set the following guidelines for forklift maintenance:
Preventive Maintenance Inspection Reports
These reports are inspection sheets that make sure the forklift is inspected properly and parts are replaced when needed. It includes a list that checks the following:
- Batteries
- Lights
- Brakes
- Doors
- Forks
- Missing or loose nuts, bolts, and belts
Scheduled Maintenance Dates
Routine maintenance helps prevent malfunction and accidents from equipment failure. Scheduling maintenance checks is a way to keep repair and replacements organized and timely.
Maintain Equipment/Use Quality Parts
Maintain equipment by keeping parts lubricated, hydraulic lines clean, replacing worn or damaged tires and brakes. Well-conditioned parts equate to less maintenance and repair work. Quality parts, simply stated, help prevent serious injuries.
OSHA requires companies to take these preventive measures to avoid injury to workers and fines due to those injuries. Failure to comply with OSHA requirements can end up costing thousands of dollars. Make sure a qualified mechanic inspects and repairs forklifts.
Why Modjoul is an important part of forklift maintenance
Modjoul is a proximity alert system that utilizes magnetic fields to provide visual and audible alerts. These alerts warn workers to the proximity of forklifts, helping them avoid potential collisions, injuries, and hazards. Keeping this system functional means a safer environment for both drivers and pedestrians.
Preventive forklift maintenance is, at its core, a strategic investment of time and money that helps your company run efficiently and predictably. Addressing minor issues through regular maintenance will prevent major problems. If you want to avoid the monetary headaches that come with delayed shipments, a disorganized warehouse, and stiff fines, make sure proper safety protocols are being followed. Your company will also enjoy the boost in employee morale generated from a strong culture based on safety. That might be the best benefit of all.