Forklifts are valuable tools. They enable businesses to work quickly and efficiently at moving and shipping products. Unfortunately, for all the benefits forklifts provide, they can also be a major threat to worker safety. However, the threat can be lessened with training, proper lighting, safety systems like proximity alert systems, and adherence to strict protocols.
One such safety protocol is the Forklift Halo Rule. This rule, when followed, curbs many of the injuries that occur from forklift accidents.
What is the Halo Rule for Forklifts?
Halo Rule: Maintains that one must always stay three feet away from forklifts. This creates a “safety halo” that consists of a two-ring zone – the danger zone and the warning zone.
Danger Zone: This is the zone within three feet of a forklift. If a pedestrian is within three feet, the operator must stop.
Warning Zone: The warning zone is located within six feet of a forklift. If a pedestrian is within six feet of a forklift, both the operator and pedestrian should make and maintain eye contact. The pedestrian then indicates their intention, and the operator is required to yield the right of way.
What Does OSHA Require for Forklift Lighting Safety?
The forklift halo can be further enhanced using visual aids such as “arc lights,” or red safety lights. The arc light’s purpose is to alert pedestrians of the rear-end swing and danger zones of a forklift. The light increases forklift visibility which helps to keep pedestrians away and creates a visible “halo” around the vehicle.
However, it’s important to note that while forklift auxiliary directional lighting is required by OSHA in dimly lit areas, attaching forklift warning lights (like halo lighting) is neither required nor prohibited.
In fact, OSHA’s General Duty clause states employers have a duty to provide a place of employment free from recognized hazards likely to cause death or severe injury. These hazards include but aren’t limited to being struck by, caught-in-between, or crushed by a forklift. OSHA considers sound-producing and visual devices appropriate ways to curb these hazards. A workplace that has these hazards but does not take steps to lower injury risks will violate the General Duty Clause.
OSHA requires forklifts operating outdoors, at night, or in areas that have pedestrian traffic to have headlights and brake/taillights. Additionally, OSHA’s Powered Industrial Truck standard states that “where appropriate to the worksite, equip trucks with additional sound producing or visual (lights/blinkers) devices. These devices include but aren’t limited to horns, motion alarms, and arc-lights.”
TIP: Setting up red halo lights? Set your halo arc further from your forklifts for additional safety. Just make sure each lift’s red lights are consistent. After all, inconsistent warning times are less safe than no warning times at all.
Forklift Aisle Width Minimums and Swing Radius
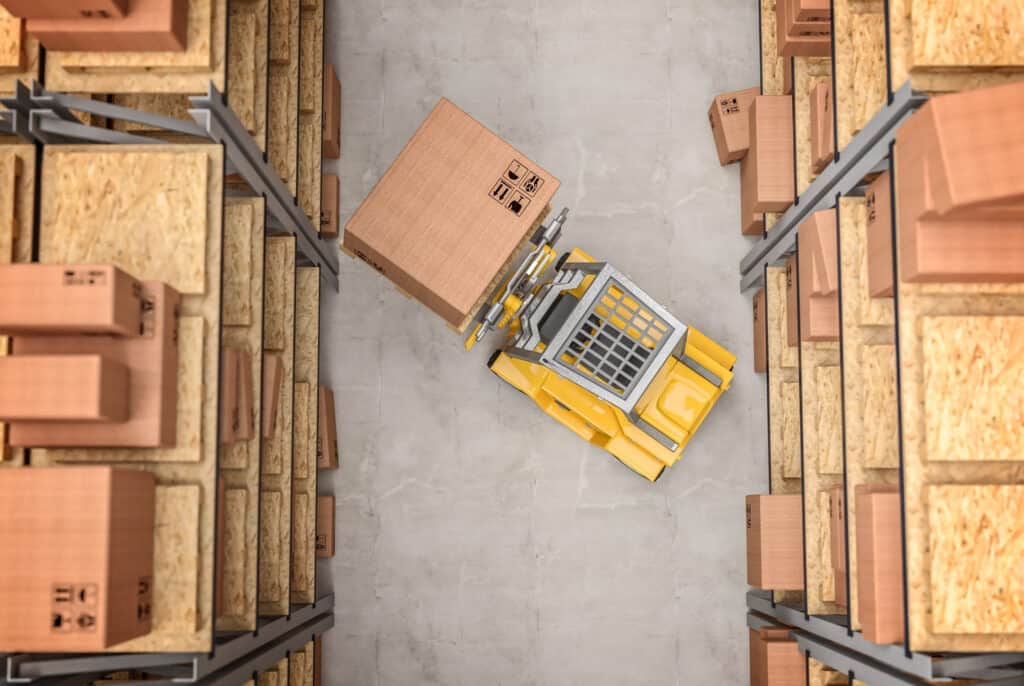
OSHA recommends aisle widths at least three feet wider than the largest equipment to be utilized or a minimum of four feet.
Forklifts, unlike automobiles, steer from the rear. This creates a forklift tail swing during turns, which moves the rear of the forklift to the opposite side of the turn. The movement creates a swing radius that can be dangerous for pedestrians, forklift operators, racks, and products. Likewise, the rear of the forklift can swing rapidly and wide, leading to the potential to crush pedestrians.
The following facts further prove the value of training and basic forklift knowledge for pedestrians and forklift operators.
- More than one million forklifts are in operation throughout the United States.
- OSHA estimates there are 110,000 forklift accidents yearly.
- One in five forklift incidents involve pedestrians.
- Over 20,000 workers are injured yearly in forklift-related accidents.
- Forklift accidents cost businesses $135,000,000 each year
- Forklift related violations are among OSHA’s top ten every year.
The Problem with the Forklift Halo Zone and How You can Improve Warehouse Safety
The problem with only using the halo zone, especially without additional aid, is human error.
No matter how well-trained the workforce or how many lists are checked, mistakes can happen. Daydreaming, complacency, sleepiness, and exhaustion can all lead to accidents. There are, however, additional tools that can be utilized to enhance general safety protocols and lessen the impact of human error.
How Forklift Proximity Sensors Can Ensure Warehouse Safety
There are two game-changing tools that can help make warehouses safer.
The first is the Modjoul HaloGuard. Modjoul is a combination SmartBelt and collision avoidance system. Both components work to help improve driver, worker, and pedestrian safety. The system uses lights, sound, and haptic (vibration) notifications to provide alerts about potential interaction risks.
Another option is the HIT-NOT proximity alert system. This system utilizes magnetic field technology to detect forklifts and pedestrians. The magnetic field passes through walls, containers, and racks to provide audible and visual alerts to pedestrians and operators.
Additional Safety Tips for Safety and Productivity
You can never be too safe around warehouse equipment. Here are some additional safety tips to make sure everyone remains safe.
- Pedestrians and forklift operators should wear high visibility vests
- If you are not able to make eye contact with the forklift operator, use a verbal alert to get the operator’s attention.
- The forklift operator must always look in the direction of travel.
- Utilize floor markings and safety signs.
- Perform a daily forklift inspection.
Don’t take your safety, or the safety of those around you, for granted. Utilize training, all available safety equipment, and good old-fashioned common sense to keep yourself and others safe. If you are unsure of how to resolve concerns in areas that include powered equipment or general safety, contact SynTech. We have over 40 years of experience creating safety solutions to fit each customer’s needs.