The Dangers of Electric Forklifts
“Can you repeat that?”
If you have asked that question in your warehouse, then chances are you work in a loud environment. Forklifts significantly contribute to warehouse noise, so many companies are investing in electric lifts. But what does the use of electric forklifts mean for workers? Are they always safer?
Forklifts enable efficient and speedy facilities, helping supply products across the world.
Manufacturers have made significant advancements to all models, including gasoline, propane, diesel, and electric. Meanwhile, the e-commerce explosion has increased pressure for timely delivery. So, there’s no wonder that warehouse owners look to lower operational costs while raising productivity. Electric forklifts are a perfect fit in this equation due to their lower maintenance cost, reduced vibration, and lower weight and noise. Even still, with all the benefits come risks.
Difference Between Gas and Electric
Gas forklifts operate on gasoline, utilizing an internal combustion engine. Think of a gas-powered car or truck. Gas forklifts operate on the same concept. These forklift types are available at a lower initial cost, can operate at full efficiency no matter the fuel level, and can be refueled in minutes. But they also release harmful carbon emissions into the air.
Electric forklifts operate on electricity. A battery supplies power and needs to be charged daily to work efficiently. Electric forklifts have lower maintenance costs due to fewer parts but are more costly upfront. They also operate at a lower noise level.
What Makes an Electric Forklift Dangerous?
Electric forklifts are downright stealthy when comparing their noise level to a gas forklift’s level. Gas-powered forklifts operate around eighty-five decibels, which is the same as a gas lawnmower according to Turf Management Systems.
Electric forklifts produce around sixty decibels or lower, which is comparable to a normal conversation between two people.
In warehouse environments, ambient noise, such as air-conditioning, workers, conveyor belts, and other machines, make an electric forklift impossible to hear. The louder the facility, the harder to hear. Wearing noise-protective headgear such as ear plugs or insulated earmuffs makes it even harder because they drain out environmental noise. Therefore, it is imperative extra precautions are taken to prevent accidents.
Forklift Accident Prevention
Blind Spots and Corners
No matter how alert or experienced a driver is, there will always be a blind spot. According to OSHA, forklift blind spots and corners of racks and walls are the leading causes of accidents. Ignoring these dangerous hazards will eventually lead to death, damaged facilities, loss of revenue, and more. Each employee/driver should follow these safety guidelines:
- Slow Down – Pretty simple, right? Mitigate the danger factor by maintaining a safe speed. Slowing down helps both pedestrians and drivers see what is up ahead.
- Utilize Pedestrian Safety Lights – Safety lights project high-intensity beams across the floor as a forklift backs down aisles, around blind spots, and comes out of trailers. These lights give pedestrians a visual cue that a forklift is nearby.
- Honk – There is always the old-fashioned yet trusty horn. Combining safety lights with the audible sound of the horn increases the chance pedestrians and other drivers are aware of another forklift’s presence.
- Modjoul – Modjoul is a forklift alert system that uses magnetic fields to provide an alert when pedestrians and other powered industrial vehicles are in the vicinity. The magnetic field passes through concrete walls, racks, and blind corner obstructions to provide audible and visual alerts to pedestrians and drivers.
Battery Maintenance and Charging Hazards
Electric forklift batteries are rated to remain in service for over 2,000 charge/discharge cycles, or five years. Proper battery maintenance may increase its life. Poorly maintained batteries lead to mechanical breakdowns, accidents, and significant injury. Here are the basic rules to follow for optimum battery life:
- Do not overcharge/undercharge the battery.
- Do not exceed manufacturer-recommended service hours.
- Don’t overwork the battery. Even if it still delivers power, change it at proper intervals.
When charging a battery, follow these protocols to maintain a safe charging area:
- Provide proper ventilation to avoid hydrogen gas buildup while charging.
- Have a foam, CO2, or dry chemical fire extinguisher.
- Do not smoke near the battery or charging station.
- Provide an eye wash station and/or drench shower.
- Post warning signs.
- Provide/have a means to communicate in the event of an emergency.
This is not an exhaustive list of precautions, but it is the minimum that anyone charging a forklift battery should keep in mind.
How To Safely Move an Electric Forklift Battery
First thing first, only trained staff should change and charge batteries in electric forklifts.
Forklift batteries are bigger than regular car or truck batteries. They can weigh hundreds of pounds. The weight alone multiplies the risk of injury and accident, emphasizing the importance of proper equipment and protocol.
- Position the truck in a secure and stable position and apply brakes before changing or charging batteries.
- Use a lifting beam or equipment that can properly lift the battery. Improper lifting equipment, such as hook chains, can damage the battery.
- Charge the battery in the designated battery charging area(s).
- Once charged, return the battery to the forklift with a lifting beam and secure it in place.
- Make sure charge indicators show a full battery.
Safeguards must be taken to prevent sparks, electrical arcs, and open flames in charging areas.
Malfunctioning vent caps can block heat dissipation, causing batteries to overheat and create harmful gas and acid emissions. Even when properly charging a battery, explosive hydrogen fumes may be produced at the end of the charging cycle. Please wear proper personal protective equipment, as contact with battery cells can cause electrical short circuits, which can burn unprotected skin.
Electric forklifts pose hazards just as any fast-moving heavy machine would. However, with quality care and safe operation, electric forklifts contribute to a less noisy and, frankly, cleaner warehouse environment due to the absence of harmful carbon monoxide and other chemical emissions.
SynTech believes safety improves productivity. We have over 40 years of experience making work sites safe for employees and are the #1 sales and service provider of the Modjoul proximity detection system. Protect your people and property by contacting the SynTech team at 256-571-5024.
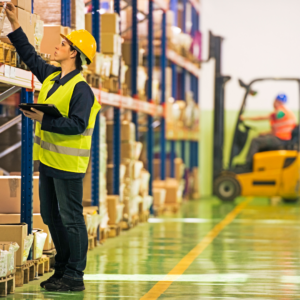