Organization, management, and standardized rules are essential components for most areas of life to run smoothly and safely.
Imagine the organization in your home. Without a housekeeping standard, dishes may end up in the bathtub and clothes in the dishwasher. Organization, in this example, could lead to family meals in the bathroom.
Similarly, a disorderly warehouse may lead to injuries, unhappy workers, and exhausted management. It’s worth putting in the effort to improve your warehouse management system efficiencies to keep your people and property safe.
Safety Hazards of An Unorganized Warehouse
The US Bureau of Labor reported 46 fatalities in the warehouse and storage industry in 2021. It doesn’t take a rocket scientist to figure warehouses can be dangerous places. To minimize injury and death, the following safety hazards must be avoided:
Badly maintained conveyor systems
Used to transport items throughout the warehouse, things can fall from a conveyor. Hair, body parts, and clothing can also become entangled.
Untrained/Inexperienced employees
Injuries, broken bones, falls, hazardous chemical injuries and death are all potential byproducts resulting from improperly trained or undertrained employees.
Improperly stacked forklift loads and storage areas
The damage that occurs when hundreds of pounds of items fall is frightening to contemplate.
Improperly stored hazardous chemicals
Burned skin, damaged lungs, and death can occur when hazardous chemicals are not appropriately marked, and proper storage systems are not in place.
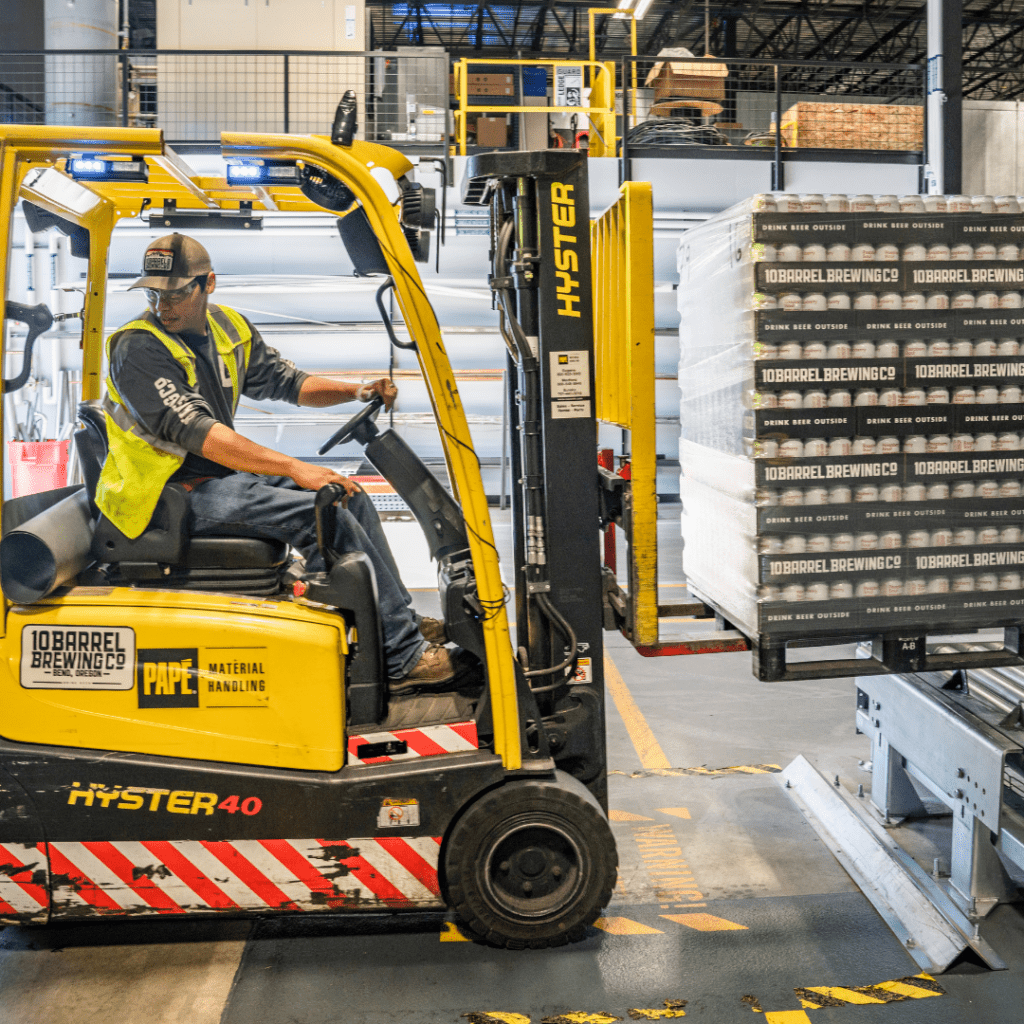
Poorly maintained vehicles
Regular servicing of powered vehicles and equipment is necessary to avoid injury to operators, people nearby, and property damage.
Docks
Employees can fall or become pinned or crushed between the loading dock and truck.
Energized equipment
If energized equipment is not properly shut off, employees may be caught between mechanical parts or electrocuted.
These hazards could become widespread when industry best practices and regulatory guidelines are not observed.
Some actions essential to sustaining a safe working environment include:
- Create an EAP (Emergency Action Plan) with instructions for employees in an emergency. The EAP should consist of exit routes, fire extinguishers, and medical station locations.
- Install conveyor safety guards and an emergency stop system.
- Train warehouse workers on proper lifting techniques and materials handling. Make sure employees understand and can perform safety procedures in case of accidents.
- Keep aisles, passageways, and floor plans clear.
- Implement training explicitly focused on properly handling, storing, and disposing hazardous materials.
- Post a written hazard communication plan throughout the warehouse.
- Use adequate ventilation within the facility to disperse harmful gases.
- Enforce safe handling of sharp objects and the usage of personal protective equipment.
- Make sure equipment operators are competent and have completed certified training.
- Conduct daily pre-shift inspections to check for controls and systems damage to equipment.
- Ensure dock edges are transparent and able to support required loads. Us warning signs and safety mechanisms to prevent someone from getting near docks while operational.
- Implement lockout/tagout programs to keep equipment from unintentional energization while undergoing maintenance.
These tips will make your organization a textbook example of safety, employee commitment, and overall efficiency.
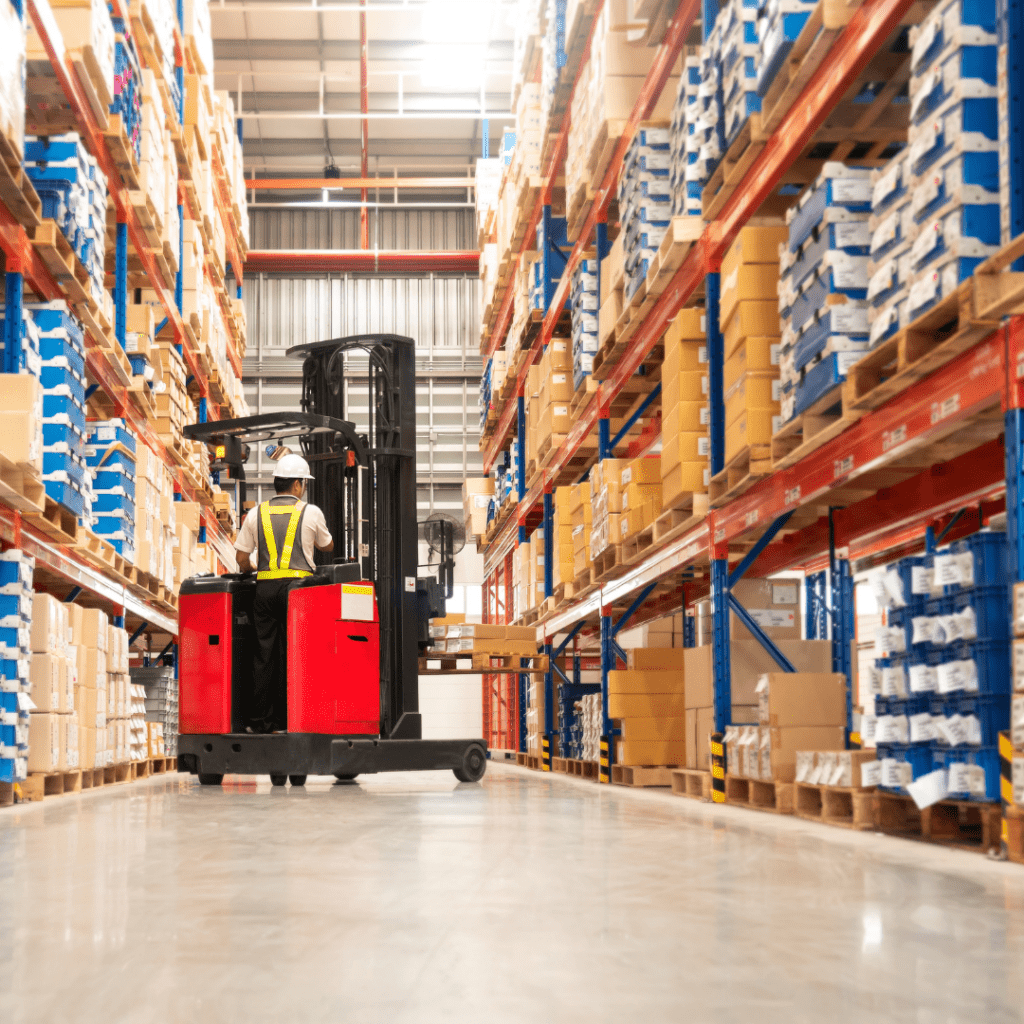
Create a More Efficient Work Environment
Grasping potential risks in the work area simplifies tackling and solving them. You can then focus on making the workplace more productive. Below are universal practices that pave the way to a more efficient environment.
Inventory management:
The process by which stock stored in a facility is accepted into the receiving area, then tracked, audited, replenished, and managed for order fulfillment.
Warehouse management:
Inventory management’s twin brother focuses on incoming/outgoing product quantities and locations and employee performance in the warehouse.
Logistics:
Effective coordination allows easy exchange between departments, maximizes policy efficiency, and smooths physical inventory flow.
Cross Training:
Aids in employees’ professional development by providing skills to perform other job duties. This helps the company prepare for unexpected situations.
Warehouse inventory management software:
A computerized warehouse inventory management system automates and simplifies w rehouse management tasks. It reveals existing stock and its specific location. It also assists in forecasting demand based on previous sales history.
Peer closely at any successful warehouse layout, and you will find these examples front and center. Accuracy and efficiency are offshoots of a “well-oiled” facility. Likewise, below are some guidelines for getting your warehouse operating in tip-top shape.
Top 5 Warehouse Organization Tips
Keep it simple. A tried-and-true methodology to eliminate waste, maximize space, and maintain a well-managed facility is the 5S system. It’s a system where there is a place for everything, and everything is in its place.
- Sort: Neat, uncluttered areas are keystones of this step. Remove unnecessary items from the area.
- Set: Keep the warehouse well organized. Identify specific storage areas and make certain materials have assigned storage space.
- Shine: Cleanliness is critical to safe environments and long-running equipment. Keep the warehouse clean and inspect work areas and equipment regularly.
- Standardize: Create uniform operations, policies, and procedures that include c consistent training and safety principles.
- Sustain: Be Disciplined. Having the discipline to meet set safety and production goals continually.
Bonus: Utilize vertical space: A warehouse’s floor space is limited. Maximize the use of the warehouse by taking advantage of the high ceilings and stacking products up to twenty feet tall.
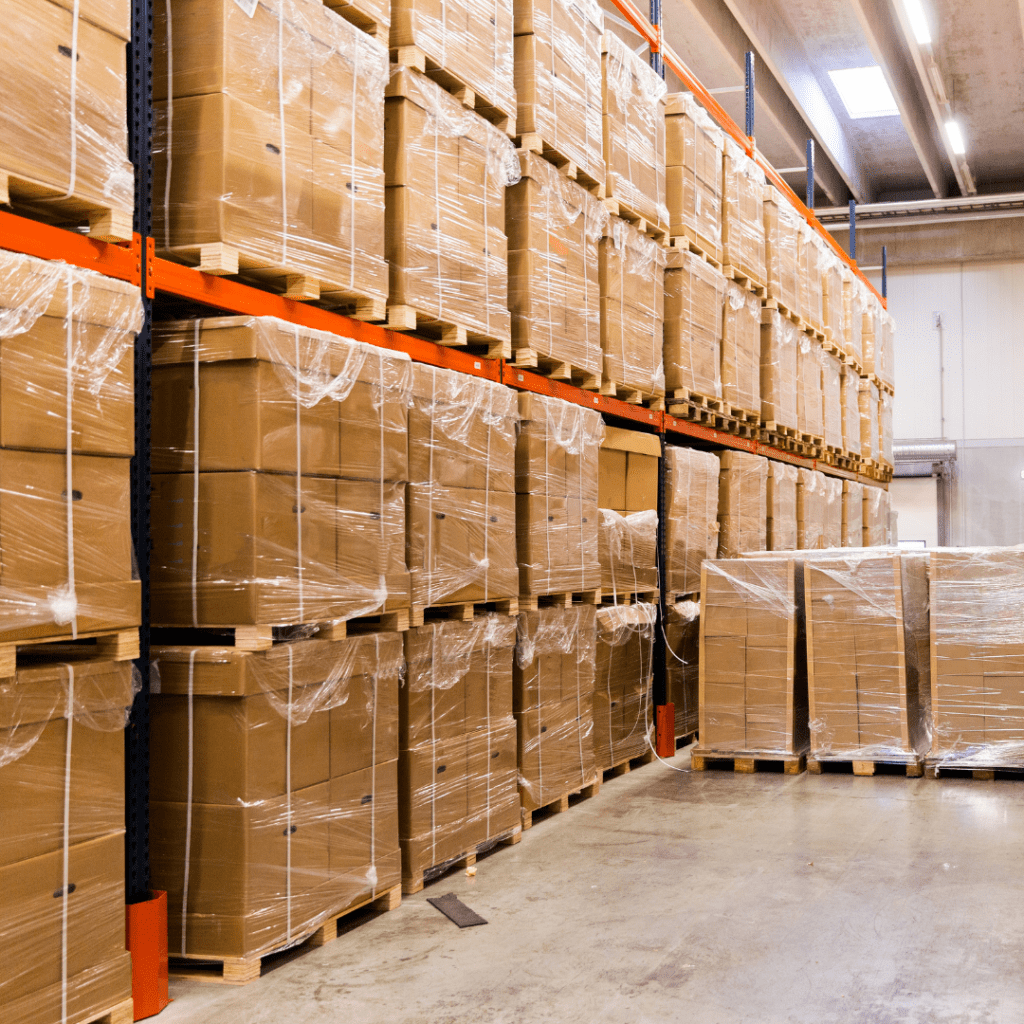
Signs of a poorly managed warehouse include having too many products, inefficient stock management, unsafe conditions, and incorrect labeling. Adopting the stated regulations will boost productivity reduce occurrences of accidents, enhance staff morale, and result in a better financial outcome.
SynTech has over forty years of experience providing training and equipment to make work sites safe. Our expertise has helped make us the #1 sales and service provider of the proximity detection system. Let us help you protect your people and property. Contact the knowledgeable SynTech team at (256) 571-5024.