A distribution center or warehouse is an essential link in a supply chain. Unfortunately, that link can easily be broken if its fleet of forklifts is inoperable.
That’s why warehouses and distribution centers use various tools to prevent forklift accidents and damage. Standard tools include seatbelts, lights, alarms, signs, floor markings, horns, and operator training. But even with those standard safeguards, The U.S. Bureau of Labor Statistics shows 90% of all forklifts will be involved in some accident at one point during their operational lifespan.
The BLS reported that in 2021, forklift accidents resulted in seventy work-related deaths. After an incident, the blame often falls squarely onto the forklift operator. Yet, considering everything an operator must do to avoid accidents, we realize many factors are at play. For instance, they must see all blind spots, avoid pedestrians, skirt past other powered industrial vehicles, operate safely around conveyors and railings, and not crash expensive forklifts into walls and stationary equipment.
Wow! Talk about pressure. This is all in addition to the standard job responsibility of moving palletized product and handling materials throughout the warehouse. There is, however, a revolutionary tool that is changing the game in forklift safety.
But before we dive into the details of that tool, let’s look at a few things that cause forklift damage and accidents.
Causes of Forklift Damage in the Warehouse
Speeding: Careless workers treat the forklift like a toy used for their amusement. It is instead a deadly, powered vehicle weighing thousands of pounds.
Narrow and Crowded aisles: This includes aisles that aren’t wide enough or too cluttered warehouse floor to enter, exit, or maneuver safely.
Poor lighting: Dim lighting makes it harder for the operator to spot obstacles and fellow workers.
Lack of training: It can’t be overstressed how vital a proper training program is to the well-being of all employees working near a forklift. Learning to operate the drive controls, the safety features, and understanding the meanings of signs and markers is imperative.
Poorly maintained forklifts: You don’t want to imagine the carnage that could ensue from a poorly maintained forklift. Do you want to be around a forklift if its hydraulic systems or other components malfunction while carrying a load? Neither do we.
In addition to avoiding the violations listed above, daily inspections and maintenance are critical to a productive and safe fleet. Check that forks are even, the overhead guard is structurally sound, the tires are in good condition, and operator controls and electrical components are responsive and operational. This is not an exhaustive list but certainly some of the most common reasons for damage.
Now, About That Tool that decreases forklift Damage
It’s called the Modjoul Proximity Detection system. It uses radio frequency or electromagnetic field technology to detect pedestrians and other vehicles.
How A Proximity Alert System Prevents Forklift Damage
These systems are unique because they offer 360° of protection, warn operators and pedestrians, and penetrate solid walls, products, machinery, and pallet racks. In addition to the advanced monitoring of equipment and pedestrians, it provides a sight and sound alarm. It is not subject to environmental or reflective interference like a traditional radio frequency infrared (RFID) system. Conventional radio frequency systems must see you to protect you. Modjoul always sees you.
Essentially, Modjoul helps prevent forklift damage because it is designed to avoid crashes.
Modjoul is the most sophisticated and precise alert system. It does not require a line of sight to detect obstacles like a traditional RFID system. On the contrary, a line-of-sight system would severely reduce Modjoul’s accident prevention capabilities. Instead, Modjoul implements a compact magnetic field generator that can be installed on all types of mobile equipment. The system also utilizes personal alarm devices (PAD) that can be worn on the hat, vest, or belt of any personnel working near forklifts. The PAD senses the magnetic field produced by the generator installed on the forklift. If a pedestrian wanders into that field, the warning systems will be alerted, allowing the pedestrian and driver time to adjust.
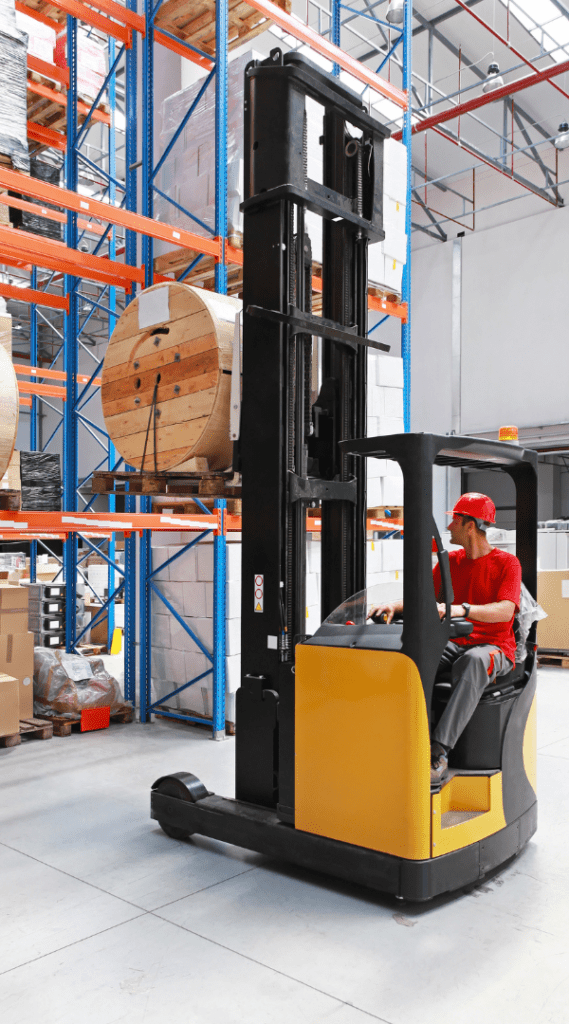
Other Ways to Prevent Damage
Rollovers, blocked lines of sight, and falling off docks or trailers are other examples where lift trucks can be damaged. Prevent these types of accidents, and others, by adhering to the safety guidelines listed below:
- Follow speed limits: Slow down, especially when rounding corners and approaching the dock.
- Don’t exceed lift capacity: Every operator and manager should know the weight limits a forklift can handle.
- Use care when raising loads: Raising and tilting the forks abruptly can cause the forklift to tip forward. Loads should only be lifted or lowered while stationary.
- Take breaks: Long shifts cause driver fatigue, boosting chances for accidents. Regular breaks are needed throughout the shift.
- Install traffic barriers: A physical barrier separating forklift traffic and pedestrians can prevent worker injury and forklift damage.
- Chock truck/trailer wheels: The weight and movement of a forklift can cause a truck or trailer to roll forward if the wheels are not secure.
- Drive with forks low to the ground: Elevated loads reduce visibility and cause tip-overs.
OSHA reports show forklift accidents tend to cause more severe injuries than other workplace accidents. The average number of days missed by a forklift accident is 13. There are an average of eight missed days for other accidents. The National Safety Council reported a mind-boggling total of 44.8 billion in wage and productivity losses due to work-related injuries in 2020.
Here’s the rub: your company doesn’t have to contribute towards those loss statistics because most forklift accidents are avoidable.
SynTech can help decrease your accident totals and increase your company’s productivity. We have over 40 years of experience providing training and equipment that has made work sites safer, and that’s why we are the #1 sales and service provider of leading proximity detection systems.
Protect your people and property by calling the knowledgeable SynTech team at (256)571-5024.