If you ever crave a visual representation of organized chaos, visit a warehouse.
You will spot heavy machinery zooming from one end of the building to the other. Hear the whirring of HVAC systems. You will see hundreds (or even thousands) of employees racing about to meet packaging and shipping quotas. See and hear computerized product sorting systems and rollercoaster-like conveyors transporting goods throughout the building.
Warehouses have an exact and surprisingly delicate balance that when broken, can cause delays, loss of revenue, or in the worst situations, injury or even death.
So, what tools can help prevent the downtime that results in revenue loss and possibly even injuries?
In this blog, we’ll explore forklift impact monitoring systems to see if they can improve your fleet management system. And we will explore if they are the best choice in modern warehouses to protect your people and property.
What is an Impact Monitoring System?
Forklift impact monitors record and track any impact caused by the forklift. The impact can occur with other lift trucks, people, walls, structures, and racking systems. It also tracks employees involved in accidents, the severity of impact, and detailed usage specific to each vehicle. The details are collected and stored electronically.
Here is a Brief List of What an Impact Monitoring System can Provide:
- Tracking of specific forklift impact/accident times.
- What shift? Does one shift have more accidents than another?
- Determine speed at moment of impact
- Monitor overall productivity of the forklift
- Record seatbelt usage
- Past and future inspections
How Impact Monitoring Benefits Fleet Management
Data collected by OSHA shows over 60,000 non-serious forklift-related accidents occur yearly. Using advanced tools, data, and training makes it possible for your company to avoid contributing to that statistic.
Impact monitoring systems record the routes of each forklift each time it is used. This enhanced visualization of when, where, and how the vehicle is used enables the development of processes to streamline traffic, improving efficiency.
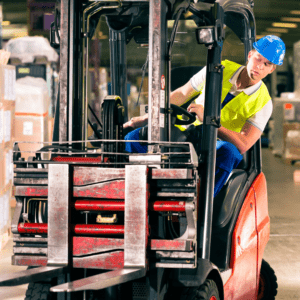
The system also:
- Monitors sudden or unusual acceleration and deceleration
- Helps optimize fleet rotations and maintenance schedules
- Collects and tracks usage data on individual operators. This data helps labor efficiency by tracking times associated with specific truck activities and tasks, including travel time, actual operational usage during work hours, traffic patterns in the warehouse, and overall run time of the forklift.
Benefits to Fleet Management Include:
- Decreases in worker injury and wasted person-hours
- Real-time data feedback
- Improved driver habits, accountability, and performance
- Greater efficiency and profitability
- Improved ability to monitor accident-prone drivers
- Optimized use of equipment
What You Can Learn from Forklift Impact Monitoring Data
A 2020 Bureau of Labor Statistics report shows a worker died every 111 minutes from a work-related injury. Thirty percent of those injuries were transportation related.
Don’t leave the safety of your workplace to chance. Warehouse safety should be priority number one for business operators and owners who value their employees and want to stay free of downtime and expensive fines.
Data compiled by implementing impact and proximity warning systems help:
- Track patterns. Is the same driver getting into accidents? Are accidents occurring at the same location?
- Determine specific violations of safety zones and safety measures
- Establish how often non-drivers are near moving vehicles and machinery
- Fix areas with restricted/poor visibility and dim lighting
- Determine blind spots and how to help drivers avoid them
- Immediately identify cause of damages sustained to equipment
- Provides a realistic approach to reducing accidents
Why Forklift Impact Monitoring Isn't Enough
The Occupational Safety and Health Administration (OSHA) estimates around 80 deaths occur yearly due to forklift accidents. Of these deaths, nearly 50% occur because of forklift struck-by accidents, pedestrians being pinned between forklift and a surface, or crushed between forklift and another vehicle.
While we would like our warehouses and workers to be safety aware at all times, the reality is that workers get distracted. A forklift impact monitoring system reduces costly collisions by encouraging safer driving practices. They can help improve operator safety by gaining valuable insight into company workflow, hazards, and the training needs you may have to prevent future accidents from occurring.
However, forklift impact monitoring systems don’t stop accidents as they are happening. To stop an accident, you need a proximity alert system.
Why a Proximity Detection System Is a Better Choice
Unlike impact monitoring systems, a proximity warning system is a sound and light alarm that alerts a forklift operator to hazards and notifies nearby workers that a forklift is operating in the area. The alarm reminds drivers and others to stop working, pay attention, and avoid unsafe areas.
The Modjoul proximity detection system is the industry’s most advanced warning system because it detects people and objects through walls, racks, and around corners. The system detects pedestrians whether they are motionless, bending over, lying down, or walking. It is an innovative system that reduces damage costs associated with collision, decreases the risk of injury and death, and protects the company’s interest by improving a facility’s overall safety
With over 40 years of experience, SynTech has become the #1 sales and service provider of the Modjoul proximity detection system. We provide training and equipment to make work sites safe. Contact the knowledgeable SynTech team at (256)571-5024. We can help you protect your people and property.